Grasping Welding WPS Requirements: Ideal Practices and Techniques for Quality Welds
In the realm of welding, understanding Welding Treatment Requirements (WPS) standards is a critical component that straight affects the top quality and stability of welds. Following these requirements makes sure consistency and dependability in welding end results. Nevertheless, accomplishing quality in welds goes beyond simply understanding the requirements; it entails implementing ideal techniques and techniques that elevate the craft to a level of precision and ability that distinguishes the standard from the remarkable. As we navigate through the ins and outs of welding WPS requirements, revealing crucial insights and strategies for achieving top-tier welds will certainly be vital for welders looking for to master their craft and create welds that stand the examination of time.
Comprehending Welding WPS Specifications
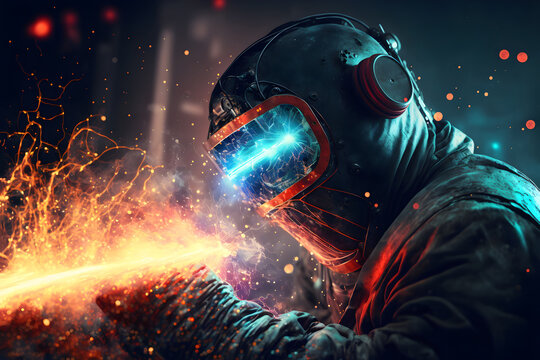
Recognizing WPS requirements is crucial for examiners, designers, and welders entailed in welding operations. By adhering to WPS guidelines, welders can create welds that meet the needed mechanical properties and architectural honesty. Inspectors rely upon WPS documentation to validate that welding treatments are being followed appropriately which the resulting welds are of premium quality. Designers use WPS standards to design welding procedures that make certain the toughness and reliability of bonded frameworks.


Necessary Tools for Top Quality Welds
Understanding welding WPS criteria is vital for welders to efficiently make use of the vital tools needed for creating top quality welds. The kind of welding device required depends on the welding procedure being utilized, such as MIG, TIG, or stick welding. Wire brushes and chipping hammers are crucial for cleansing the weld joint prior to and after welding to get rid of any pollutants that can affect the top quality of the weld.
Key Methods for Welding Success
To achieve welding success, one have to master the key techniques essential for creating high-quality welds. One crucial strategy is maintaining the correct arc size. Keeping the electrode at the optimum distance from the workpiece is essential for developing solid, consistent welds. In addition, regulating the travel rate is extremely important. Moving too rapidly can result in inadequate infiltration, while relocating too slowly can lead to extreme heat input and potential flaws. Correct manipulation of the electrode angle is another important strategy. The angle at which the electrode is held can affect the grain shape and penetration of the weld. Additionally, ensuring regular gun angle and instructions of travel is important for harmony in the weld bead. Lastly, keeping a stable hand and a steady welding setting throughout the procedure is crucial to attaining accuracy and consistency in the welds. By mastering these crucial strategies, welders can elevate the high quality of their job and achieve welding success.
Ensuring Compliance With WPS Criteria
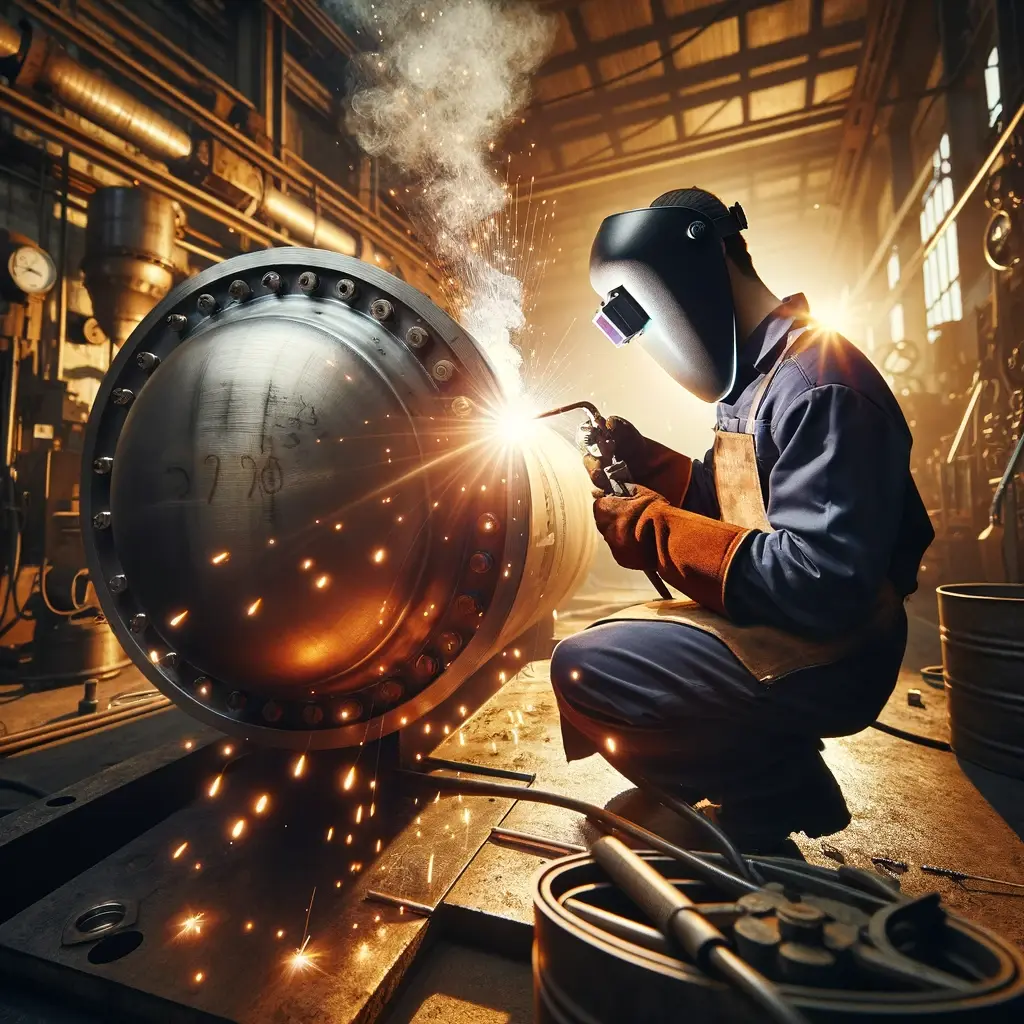
In addition, welders should undertake training to familiarize themselves with the WPS Recommended Reading standards pertinent to their work. Routine audits and inspections need to be carried out to verify that welding tasks line up with the prescribed WPS standards. Furthermore, maintaining in-depth records of welding criteria, devices calibration, and examination results is essential for showing compliance with WPS standards - welding WPS. By carefully adhering to WPS criteria, welders can guarantee that their job satisfies the needed high quality degrees and adds to the overall success of the welding job.
Troubleshooting Common Welding Issues
When confronted with common welding issues, recognizing the origin is important for reliable troubleshooting. One common problem is the existence of porosity in welds, frequently triggered by pollutants such as oil, moisture, or rust. To address this, guaranteeing appropriate cleansing of the base steel prior to welding and using the appropriate protecting gas can dramatically reduce Click This Link porosity. Another issue often experienced is absence of blend, where the weld fails to properly bond with the base material. This can stem from inadequate warm input or incorrect welding method. Changing specifications such as voltage, cord feed rate, or take a trip rate can assist enhance fusion. Furthermore, distortion, fracturing, and spatter prevail welding difficulties that can be mitigated with appropriate joint prep work, constant warm control, and choosing the suitable welding consumables. By completely understanding these usual welding issues and their source, welders can effectively troubleshoot troubles and attain high-quality welds.
Verdict
In final thought, grasping welding WPS requirements requires an extensive understanding of the guidelines, utilizing necessary devices, and applying vital strategies for effective welds. Making sure conformity with WPS requirements is essential for producing quality welds and staying clear of common welding problems. By following finest techniques and methods, welders can accomplish trusted and consistent results in their welding jobs.
In the world of welding, mastering Welding Treatment Specification (WPS) criteria is an essential part that straight affects the quality and stability of welds.When diving into the world of welding practices, a crucial element to comprehend is the importance and ins and outs of Welding Treatment Specification (WPS) requirements. WPS criteria provide a comprehensive standard for welding procedures, making certain consistency, quality, and safety and security in the welding process. The type of welding maker required depends on the welding procedure being made use of, such as MIG, TIG, or stick welding.Achieving welding success with the mastery of essential methods requires a detailed understanding and adherence to Welding Treatment Specification (WPS) standards.
Comments on “Welding WPS: Typical Errors to Prevent and Exactly How to Correct Them”